Which configuration should be used? Is Close Coupled better than Long Coupled or vice versa? Unfortunately, these questions are often answered from the perspective of the supplier. That is the supplier will prefer to supply one or the other depending on their business model. But is this in the best interests of the end user? This discussion paper seeks to address these questions from an independent perspective without bias.
Lets begin with some definitions. Long coupled or Close coupled refers to the method of connecting the motor to the pump. Long coupled refers to a Bareshaft BPO pump and electric motor mounted independently on a base and connected via a spacer coupling. Close Coupled refers to the design of an intermediate yoke which allows the pump to have a direct connection to a standard metric frame flanged electric motor. Commonly refer to as Motor-pumps.
It has been long standing convention in the HVAC market to supply long coupled pumpsets for chilled and condenser water reticulation. The long coupled pumpset has been challenged in recent years with increasing preference towards Close Coupled pumps. This has been driven partly by the pump companies preferring to sell a box product and partly by site managers who prefer this style as it removes the requirement of laser alignment.
The main advantages of the both configurations can be summarised as follows: –
Close Coupled configuration:
- Compact design saving space in your plantroom – up to 30% reduced floor space.
- Back Pull-Out Feature is retained with the close coupled pumps – repairs and inspections can still be performed without dislodging pipework.
- Close coupled pumps such as BakerBloc still utilise standard metric frame motors, which are readily available in multiple brands across the country minimising downtime in the event of motor failure.
- Once delivered to site and installed, there is no need to have the coupling alignment checked. This allows your site manager to continue with the flushing, start up and commissioning of the system without having to coordinate the pump technician, thus streamlining the whole operation.
- Close coupled pumps enable smaller inertia bases giving cost savings of base as well as less concrete required – less carbon footprint.
- Reduced maintenance – 2 bearings instead of 4.
- When incorporated into prefab units, the overall size will be smaller than if a long coupled style is utilised in the prefab.
Long Coupled configuration:
- Servicing the pump can be easier – seal replacement and bearing changes can be managed without having to touch the motor
- Motor bearing replacement can be done without having to dismantle the pump, and thereby incur the cost of the replacing the pump seal as would be the case in a close coupled pump.
- The Back Pull Out feature (BPO) is never compromised with long coupled pumpset due to the spacer coupling, whereas base design on a close coupled pump can be an issue. More on this below.
- Some brands of close coupled pumps do not allow for a change of impellers as they are matched to the motor size thereby giving no room for adjustment of flow or pressure in the future.
THINGS TO WATCH – Close Coupled
There are two main pitfalls to look out for when assessing the use of Close Coupled options.
- Are the offered pumps fitted with standard metric frame motors? Some motor pumps are factory fitted with a motor produced by the pump manufacturer in Europe that is unique to the pump resulting in expensive replacement and potentially extended lead times.
- Is the base design such that the Back Pull Out feature is not compromised? Does the base design/length allow for the easy sliding back of the motor for servicing? See Figure 1.
THINGS TO WATCH – Long Coupled
- Does the plant area allow for long coupled pumps? Are there any limitations that would have an impact on special access around the pumpset?
- Does the end user already have other long coupled units on their HVAC plant? If so the ability to interchange elements in breakdown situations can be of great benefit.
- How large are the electric motors?
MAINTENANCE – DOES IT MATTER?
Consideration should be given to the size of the electric motor on the pumpset in question. Normally, the larger the motor size, the greater the maintenance challenge. For this reason, preference may be given for a separate motor mounting as is the case with a Long Coupled pumpset. That being said, maintenance can still be a streamline operation if forethought is given to the placement of overhead fixture for installing a block & tackle when servicing is required. This feature should be considered in the early stages of design.
HOW TO DECIDE
The FLOW CHART below in Figure 2 illustrates the important steps in the decision process of Close and Long Coupled pump. It serves as a summary of the above and we trust you find it helpful.
As always, Masterflow welcomes your comments and feedback. Please send us your thoughts by the Contact Us form.
Figure 1:
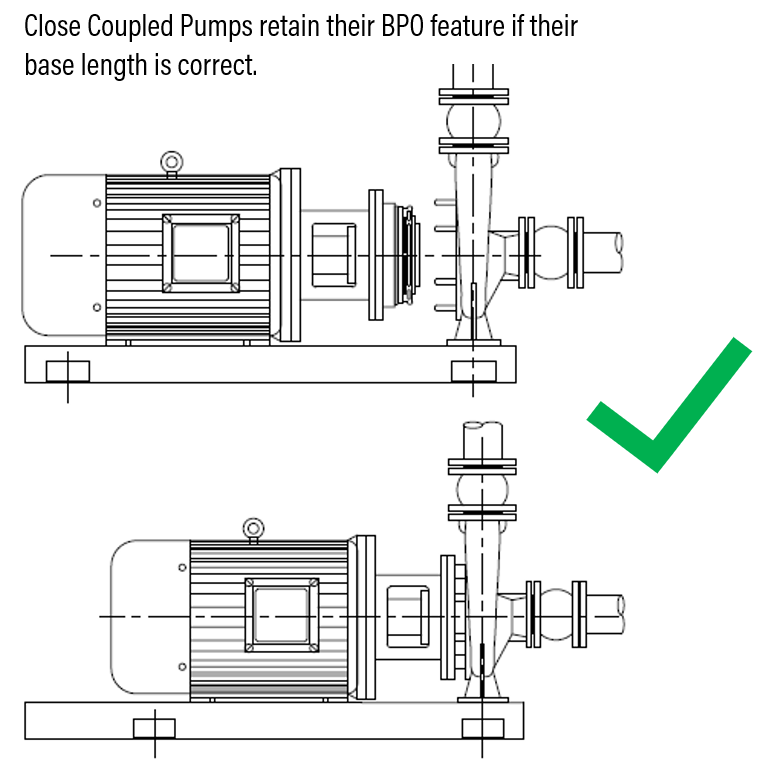
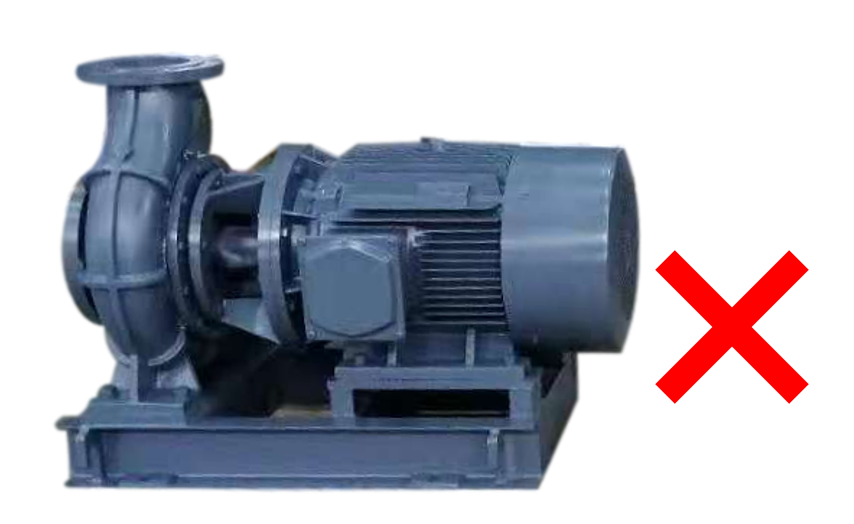
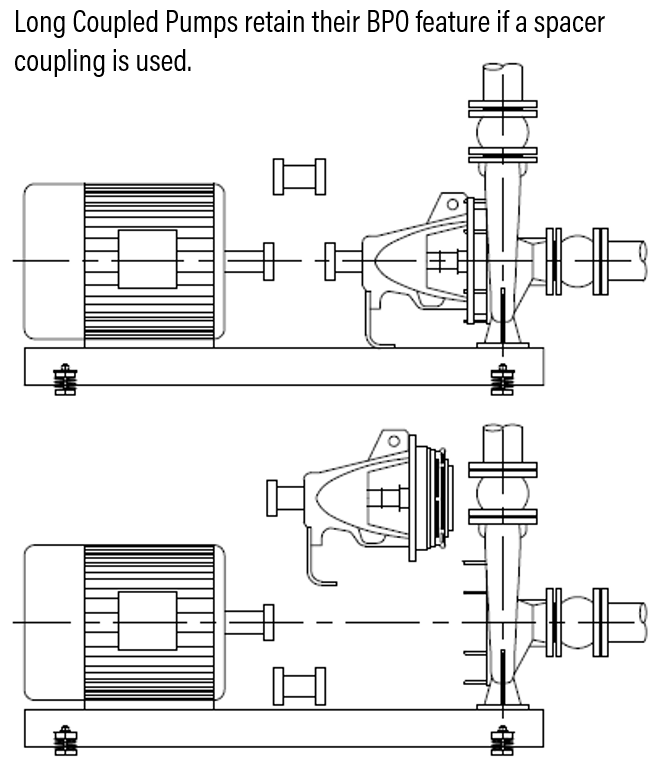
Figure 2:
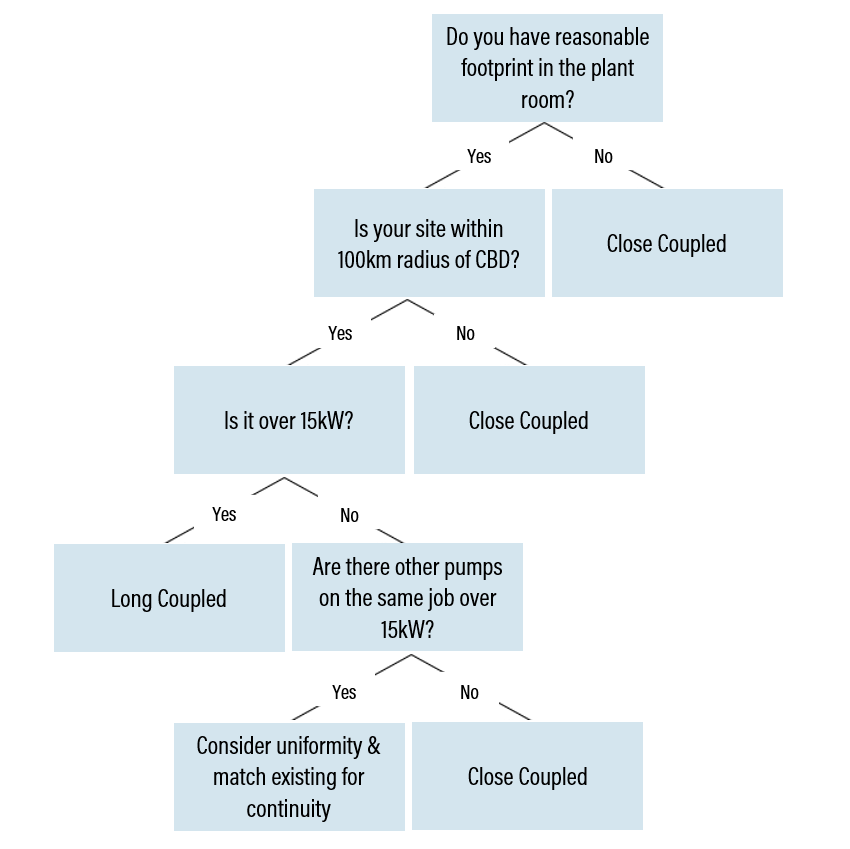